Development of Autonomous Flight Drones for Tunnel Inspection
Successful Verification of Obstacle Avoidance Flight with Non-SLAM Autonomous Drones Pursuing High-Speed Flight
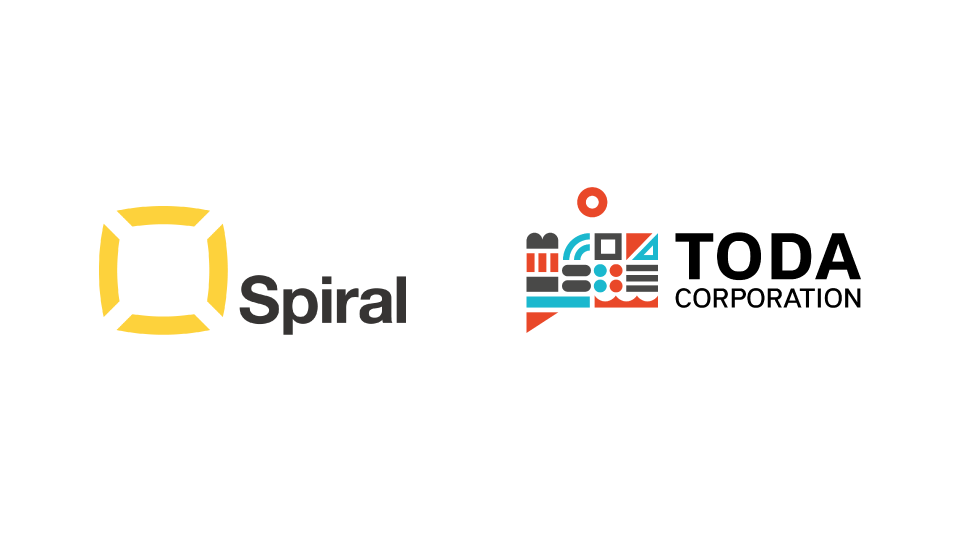
Spiral Inc. (Headquarters: Tokyo, President: Tomohiro Ishikawa) and Toda Construction Co., Ltd. (Headquarters: Tokyo, President: Seisuke Oya) jointly developed a “Non-SLAM※1 Autonomous Flying Drone”※2 equipped with obstacle detection sensors at the end of October 2023. The collaborative project involved conducting flight verification in a full-scale tunnel located in Tsukuba City, Ibaraki※3. As a result, it was demonstrated that the drone could automatically detect obstacles and navigate safely, even in environments with no access to GNSS※ (Global Navigation Satellite System) where heavy machinery congestion occurs.
In an effort to enhance safety and productivity in mountain tunnel construction, both companies will continue on-site demonstrations with autonomous flying drones, targeting full-scale deployment in actual construction sites by the fiscal year 2025.
- 1 SLAM: Simultaneous Localization and Mapping, a technology that performs self-positioning and surrounding map creation from the distances and directions of feature points simultaneously.
- 2 Non-SLAM Autonomous Flying Drone: A system that enables autonomous flight using only drones and markers with flying instructions recognized by cameras mounted on the drone, without relying on SLAM technology.
- 3 GNSS: A system that uses artificial satellites to measure positions with high accuracy.
Background and Challenges
In the Japanese construction industry, workforce shortages due to an aging population and the necessity for disaster prevention in high-risk areas pose significant challenges. The demand for efficiency in visual inspections and measurements has surged. Spiral and Toda Construction have conducted three drone demonstrations to automate data acquisition in non-GNSS environments like mountain tunnels.(※4) These trials focused on image-based data acquisition and facility location identification within tunnels, preparing for real-world deployment※4. To address dynamic environments with shifting heavy machinery, the joint development now incorporates “obstacle detection sensors” on drones, aiming to enhance automation in tunnel data acquisition.
In this experiment, flights using a drone equipped with obstacle detection sensors and an obstacle avoidance system were conducted in the actual tunnel testing facility in Tsukuba City, Ibaraki Prefecture, addressing challenges posed by changing environments.
- 4 Toda Construction Press Release (March 16, 2023): Verification of 3D Coordinate Acquisition in Tunnels Using Non-SLAM Autonomous Flying Drones
https://www.toda.co.jp/news/2023/20230316_003183.html
System Features
The control mechanism for autonomous flight utilized Spiral’s “MarkFlexAir (MFA)※5.”
The system features include:
- Drone and markers enable autonomous flight, eliminating the need for pilot or remote-control system intervention, preventing accidents caused by communication failures.
- Obstacle detection sensors automatically identify and avoid obstacles while maintaining the designated flight path.
- Captured images (4K/30fps) can be uploaded to a dedicated application via Wi-Fi.
- The system operates without SLAM technology, allowing autonomous flight in low-light areas with few features, facilitating high-speed, long-distance flights in dark and obstacle-rich environments like mountain tunnels.
- 5 MFA: MarkFlexAir, Spiral’s patented technology enabling autonomous drone flight without GNSS, using markers.
Verification Overview
In this verification, we utilized a drone equipped with obstacle detection sensors for autonomous flight within the real tunnel test facility to confirm flight stability and image acquisition. As a result, we successfully achieved a speed of 7 km/h over a 1800m distance. During obstacle avoidance flights, the drone successfully navigated through the designated flight path while avoiding installed obstacles, confirming the proper operation of the obstacle detection sensors.
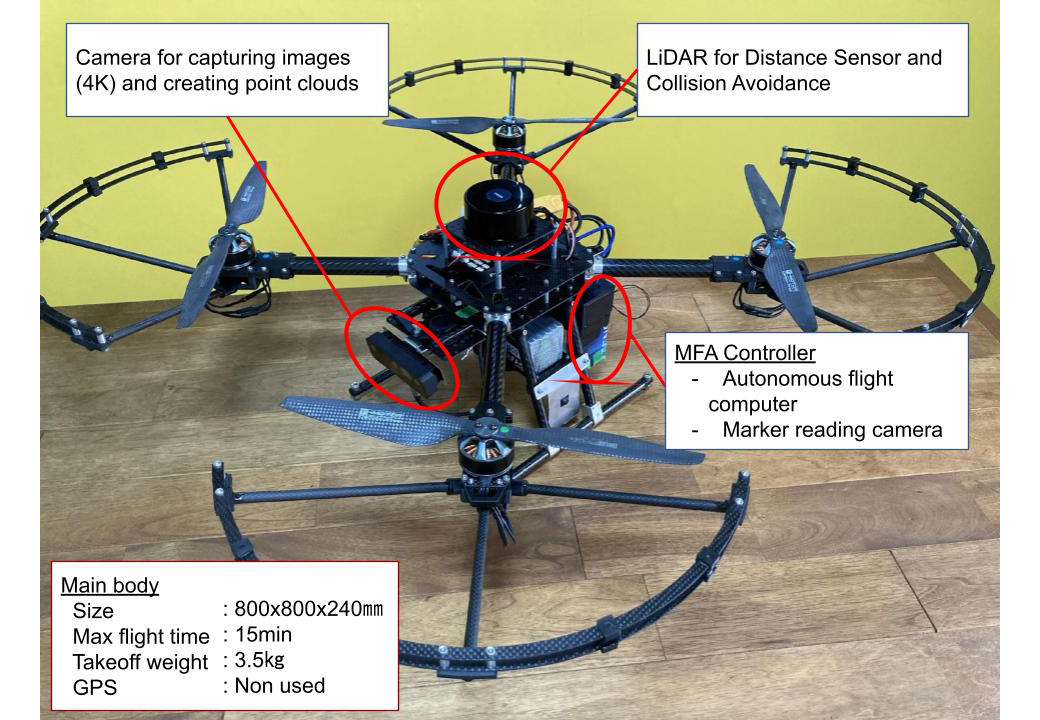
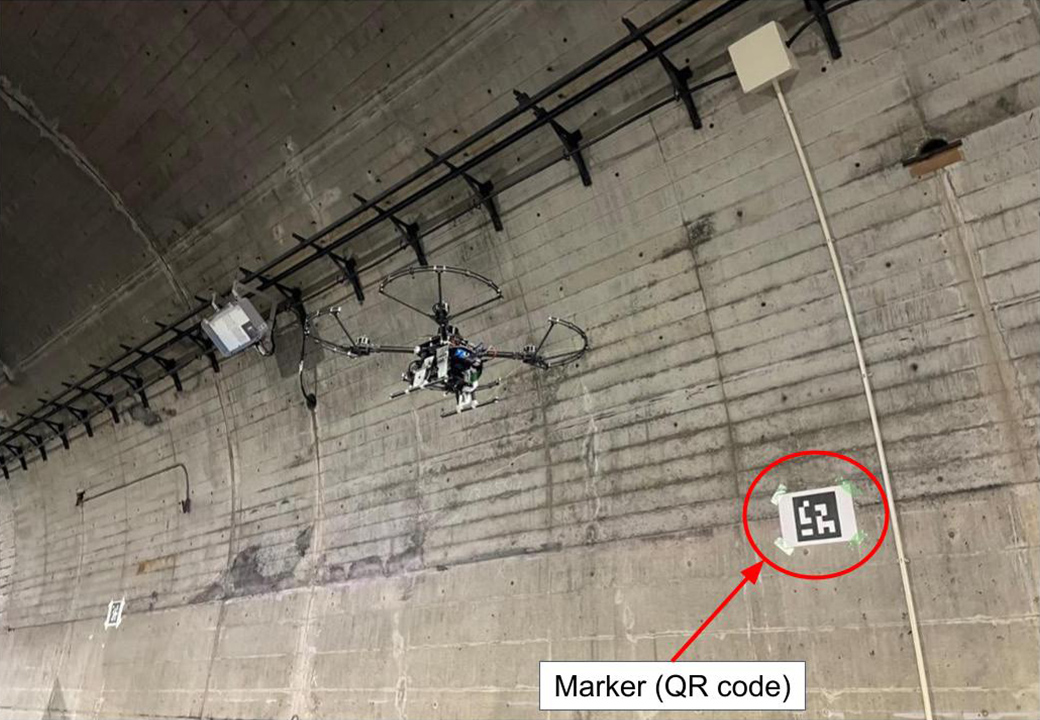
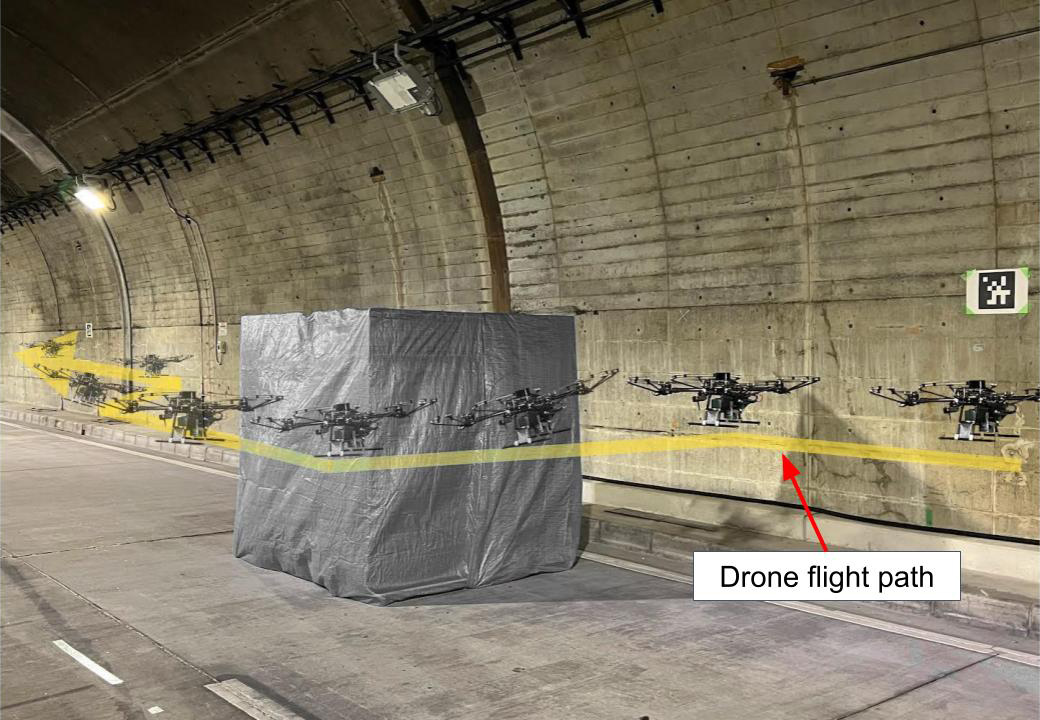
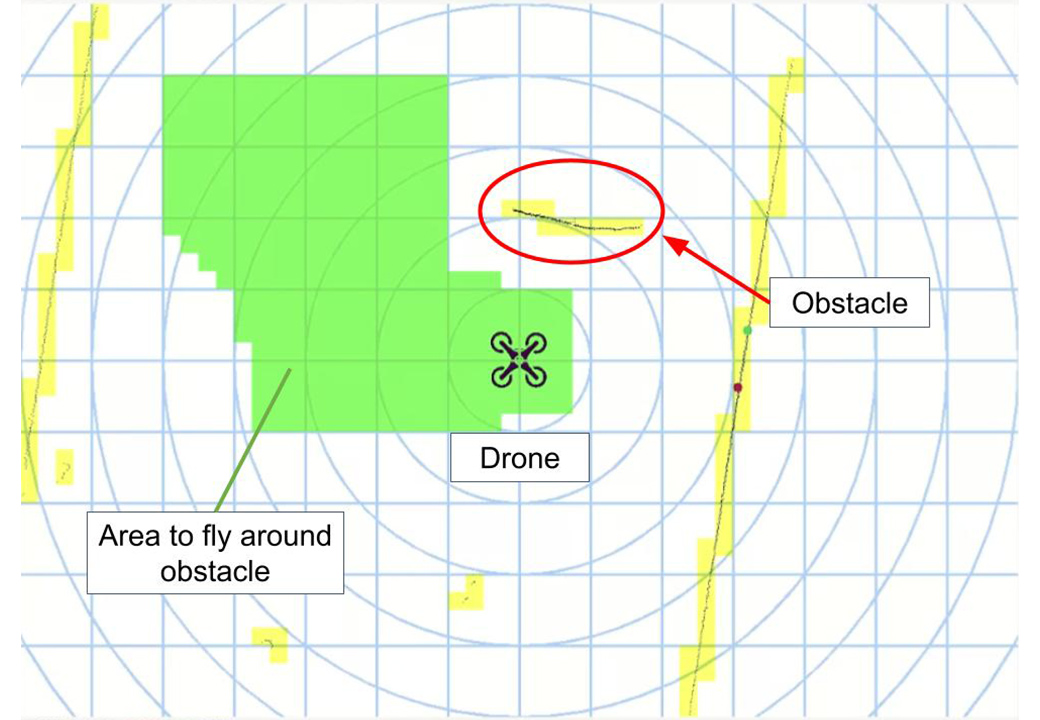
Future Outlook
With the positive results confirming the stable flight of non-SLAM autonomous flying drones and the accuracy of obstacle detection sensors, practicality is expected to further increase in actual construction sites where various machineries are congested. This will lead to the precision enhancement of information acquisition within tunnel excavations.
For future development, we will continue researching and improving the impact of external disturbances on obstacle detection sensors in real-world environments and design measures to avoid false activations. We aim to achieve further precision improvements and conduct trial operations, with the goal of commencing full-scale deployment at tunnel construction sites by the fiscal year 2025.
About Global Expansion
Spiral is currently in the process of establishing an entity in Vienna, Austria. Having successfully started multiple startup accelerator programs throughout Europe, we aim to align our initiatives with the safety, efficiency, and agility inherent in the construction industry. Concurrently, we are actively seeking partnerships across Europe to facilitate Proof of Concept (PoC) projects for the seamless implementation of our cutting-edge autonomous drone solutions.
Spiral Selected for Austrian accelerating program, focusing on deep tech Startups.
Link: https://spiral-robotics.com/en/news/231227
For Further inquiries,
please contact
Miyu Nishihira
Global Marketing Manager, Spiral Inc.